WIND TURBINE COMPONENTS
Kirkholm has worked on projects within wind energy and the wind turbine industry for more than a decade. Wind turbines are built to last and operate for many years, which is why it is important to ensure their strength and durability. In this case, we show the advantages of doing this via structural calculations on wind turbine components precisely to ensure their strength and durability through transport, installation and operation.
Structural calculation of wind turbine components
- transport loads, installation loads and operational loads
Components and structures for wind turbines are exposed to many different loads - it starts from the moment the structure leaves the production hall and is transported to the site, where it will help keep the wind turbine in operation for the next 20-25 years.
Durability and reliability of wind turbines
For many years, Kirkholm has worked with structural simulations to document the strength according to current standards. The size of the models varies greatly from larger structural units to smaller components such as bolted joints, welds, nacelle, tower, foundation and heavy test structures. Regardless of the size, the models always contain their specific complexities when they need to be analyzed.
Different load scenarios on the components mean that there will be areas and details that will be challenged. Therefore, it often requires a number of design iterations to ensure that each and every joint is strong enough and that the overall structure has the desired stiffness and strength.
In the following we will look at a number of load scenarios and situations that are often current when it comes to wind turbine components in order to concretize our approach to working with structural calculations:
TRANSPORT
- Lifting the component from A to B with a forklift or a crane: Here, the strength of lifting eyes and the surrounding structure will be in focus. But the overall structure must also be able to absorb the forces from the lifting points, so that, for example, folding does not occur in the structure. Transport of the component by train, truck or ship: Transport analyzes are carried out here, where accelerations and shock effects are applied to the structure to simulate the individual modes of transport. Lashing of the components on the means of transport is an important part of this analysis. Lashing elements such as chains that can only absorb tensile forces can be simulated in Ansys Mechanical. If a structure has to be transported horizontally in relation to the normal operating position, it often presents a number of structural challenges, where the structure must also be dimensioned for this scenario.
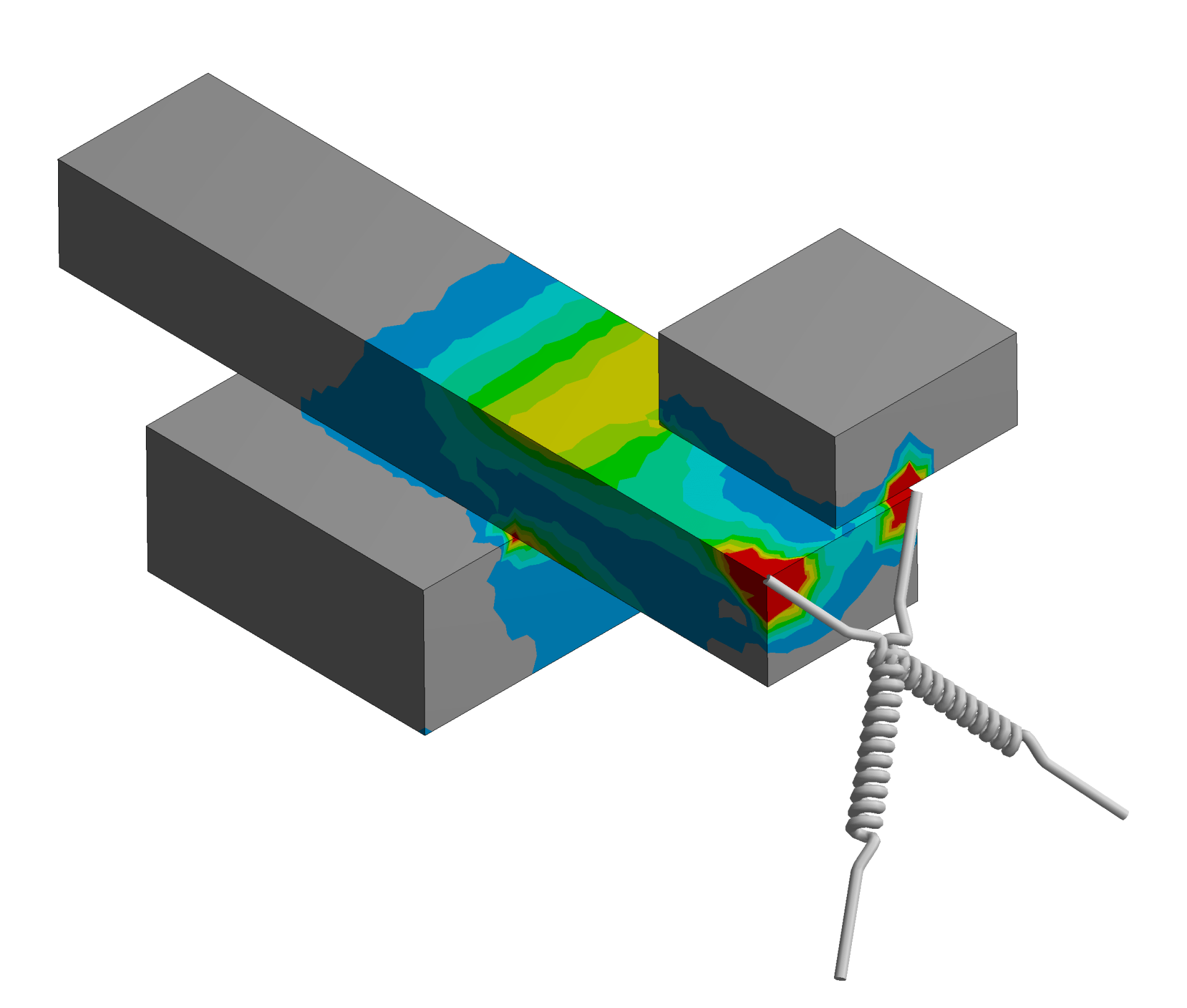
INSTALLATION
- When the individual components arrive at the site and are to be installed in the wind turbine, this generally happens via different types of bolted joints. Kirkholm often works with calculations of these joints, as many of them are often strongly affected by fatigue. Simulation and calculation of bolted joints require defining the actual conditions as precisely as possible, so that the prestressed bolts, the substrate and friction conditions are accurately described. Depending on the desired level of detail, the bolts are simulated as solid models or as beam elements. Nonlinear contacts often become part of the necessary simulation model, resulting in many hours of simulation.
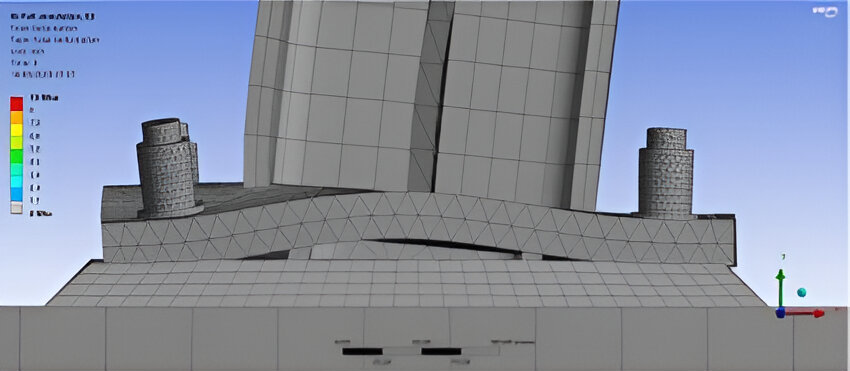
OPERATION
- Many wind turbine components consist of both welded and bolted joints, which are exposed to fatigue loads during operation. To ensure that the welded joints appear with the correct stiffness in the construction, the geometry of the welding is often included in the model. This helps to provide a detailed picture of stress distribution and concentration of stress. These detailed analyzes help to ensure that the welds can withstand both static and dynamic influences for many years. Eurocode 3 is often used as a starting point for evaluating the simulations to dimension both bolted and welded joints according to current standards, so that the calculation verification can be approved by a third party. This could, for example, be DNV-GL, which must certify the documentation afterwards, which of course places specific demands on the quality of the calculation documentation. Wind turbines are in a dynamic environment with many vibrations, which the wind turbine's components must be able to absorb without cracking. Natural frequency analyzes therefore play a large role in the design, as both weight and stiffness must be correctly matched. The natural frequency spectrum of a structure can be calculated using Finite Element analyses. In this way, it is possible to avoid natural frequencies in the structure coinciding with the operating frequencies of the wind turbine and thereby avoid undesirable resonance phenomena.
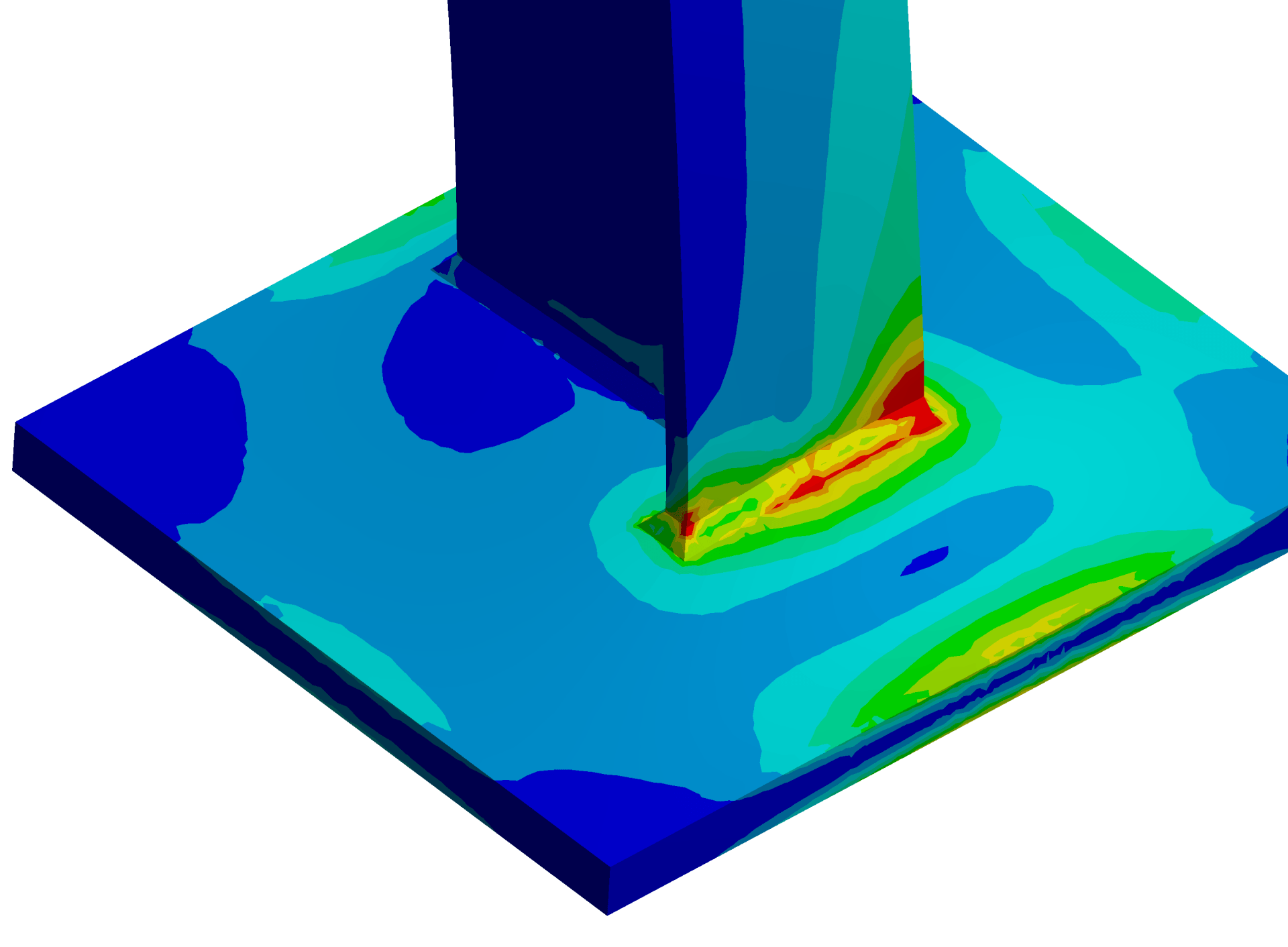
COMMUNICATION AND ITERATIONS ARE IMPORTANT
It is important that in these projects there is close collaboration between the engineers who design and those who work to perform the structural calculations to ensure that the design and calculation iterations proceed quickly and efficiently.
Although you can often start from an existing design and thus have a good starting point, it will be difficult to envisage all the above load cases early in the project. Thus, iterations on the design of the construction are part of the process. The number of iterations depends on the level to which one wants to optimize one's design, which is often governed by the established requirement specification on the structure.
The communication of most construction details continues to take place via 2D drawings. It is therefore important that all significant details determined by the structural calculations are noted correctly on the 2D drawings.
It is therefore of great value that there is good communication between all parties and that thorough quality assurance is carried out on the drawings before they go into production. In the prototype phase, there will often be a need for adaptations of construction details, which may require adaptation of calculations, design and 2D drawings.
It is a pleasure for Kirkholm to be part of these projects, and there is always room for further optimization. We look forward to the next major structural projects, and are happy to have an initial meeting to share our experiences. Our many years of experience have contributed to the fact that we have been through virtually every aspect of the wind turbine industry. You can read more about which tasks Kirkholm has worked on, among other things, when it comes to wind energy and the wind turbine industry right here.
Do you have questions, does an initial meeting sound interesting or would you like to know more about how Kirkholm works with Finite Element and our competencies within wind energy and the wind turbine industry? Then we would like to offer a non-binding chat. Use the contact form or get hold of our CSO Nicolai, who has, among other things, 10 years of experience from the wind turbine industry: